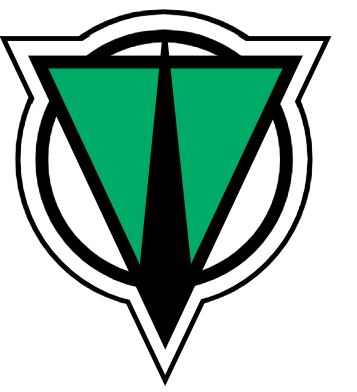
The construction sector suffered the weakest increase in average earnings in 2024 compared to all other industries, experiencing just 3% growth in regular pay compared to a 5.6% average. Total pay growth including bonuses in construction was even lower at 1.7% annually.
As a result, a survey revealed that ⅓ of tradespeople are refraining from purchasing new tools and 13% admit to using tools which aren’t in their peak condition due to cost concerns.
Protrade, a leading UK supplier of professional power tools, has sought to find a solution by gathering new data to highlight where investing in tool repair can lead to substantial savings for tradespeople.
With the average tradesperson spending £2,592 on new tools every three years, the data reveals potential savings can be made through the upkeep and repair of professional tools, providing a more affordable and sustainable option.
Tool experts suggest that certain premium tools should be serviced at a qualified tool repair centre at least once a year to ensure they work at optimal levels. If a repair is necessary, it will extend the tool’s lifespan, and early diagnosis accompanied with replacement of items like bushings and bearings, can lead to long-term cost savings.
Based on this, Protrade has calculated how many times it is cost-effective to repair a tool before tradespeople are better off buying a new one.
Protrade’s analysis shows that on average, plunge saws, drywall sanders and hammer breakers can be repaired up to 5 times before they become more cost-efficient to buy a new one. Petrol cut off saws are the next most cost-efficient items to repair, with tradespeople being able to extend the lifespan of this tool through servicing and repairs up to 4 times before it’s better to buy new. The least cost-effective tool in the analysis was the ½” router, but it was still worth repairing twice before replacing.
With the advent of cordless power tools, and the ability to purchase body only tools, with no batteries and chargers, making the replacement cost significantly less – certain lower value items such as drills, impact drivers and angle grinders simply are not worth repairing.
The average repair costs don’t factor in tool warranties, which typically provide a standard three-year guarantee on new tools from most manufacturers, covering repair costs during that time, which provides further significant savings to tradespeople when taken full advantage of.
Craig Sanders, Joint Managing Director at Protrade, said: “Tools are people’s livelihood, and the ongoing cost of living crisis is only making the challenge of affording new tools more acute.
“Our analysis shows that certain tools offer much better value when repaired rather than replaced. Drywall sanders, hammer breakers and plunge saws top the list for repair-worthiness.
“The key is to know which tools give you the best bang for your buck when repaired, and proper servicing requires the right training. Investing in quality repairs leads to long-term savings and enhanced safety. This data empowers tradespeople to make informed choices about when to repair or replace their tools, potentially saving hundreds of pounds across their toolkit.”
“Warranties provide additional savings, and since less than 25% of customers register their tools, we handle the warranty registration process to ensure they don’t miss out on any potential benefits.”
16% of tradespeople are attempting to fix power tools themselves
“Significant dangers are involved with attempting to repair specialist equipment without access to manufacturer support, relevant training and equipment”, warns Sanders, “it’s important we are raising awareness of the dangers associated with repairing your own power tools without the proper qualifications, training and diagnostic tools from manufacturers.
“Improper repairs can lead to serious injuries and can also compromise a tool’s safety features, increasing the risk of future accidents and incurring more expensive future repair costs.
“Using manufacturer-supplied OEM replacement parts is critically important for safe tool repair. These parts are often only available through authorised repair centres, like our own, and are crucial for ensuring safety. There is a significant danger associated with using non-standard parts and particularly with counterfeit batteries – using these parts can lead to tools catching fire or even exploding due to the absence of essential protection mechanisms.”
How tradespeople can make their tools last longer, according to tool maintenance experts at Protrade
Craig Sanders shares his top tips:
- Regular tool repair and maintenance at a professional service centre at least once a year can help maintain their condition, avoid costly downtime, unexpected repair bills and expenditure on new tools.
- Customers should look to invest in durable tools made of high-quality materials, such as fibreglass-reinforced plastics and metal components, as well as tools with IP ratings and compliance with relevant safety standards.
- Buying tools from reputable manufacturers with longer warranty periods can significantly minimise costs. The average warranty for power tools can range from one to three years depending on the brand. Protrade offers a robust three-year warranty on most power tools without the need to register, and additional extended guarantee beyond the manufacturers standard conditions, as part of their “#BuiltOnTrust”program with preferred partners.
- When purchasing Milwaukee power tools, only ever buy from a Milwaukee Authorised Distributor. From 1stFebruary 2024, Milwaukee prohibited all dealers from selling their brand on marketplaces such as Amazon and eBay, and any tools not supplied by an Authorised Milwaukee Distributor would not be eligible for their full extended guarantee period.
- Keeping blades sharp in saws. When the cutting edge dulls, users tend to put more pressure on to achieve the cut, and this stresses the motor and bearings.
- Consult the manufacturer’s instruction guide to identify any recommended routine care and maintenance tips.
- Clean tools at the end of each day to ensure that vents and surfaces remain clear. This can also help prevent grime from working its way into the tool’s internal mechanisms.
- Store tools in dedicated, dry areas, particularly batteries. This will help to prevent damage caused by collision with other items and corrosion on electrical components. Silica gel pouches can also help with this. Ensure batteries in particular, don’t get wet.
- Lubricate as instructed. Use grease or other lube as specified by the manufacturer to combat overheating, corrosion, and prolong the life of the moving parts. When using SDS hammer drill bits, grease the end where metal-on-metal movement occurs.
Finally, to minimise repair downtimes and hassle, only purchase your power tools from a supplier with an in-house service facility.
Methodology:
The average cost of new tools in 2024 was calculated by averaging the prices of tools from all manufacturers supplied by Protrade. The average tool repair costs were determined by analysing repair receipts for each corresponding tool received at Protrade’s service centre from 2023-2024.
To figure out how many times a tool can be repaired before it becomes more efficient to purchase new, the new tool cost was divided by the average repair cost.