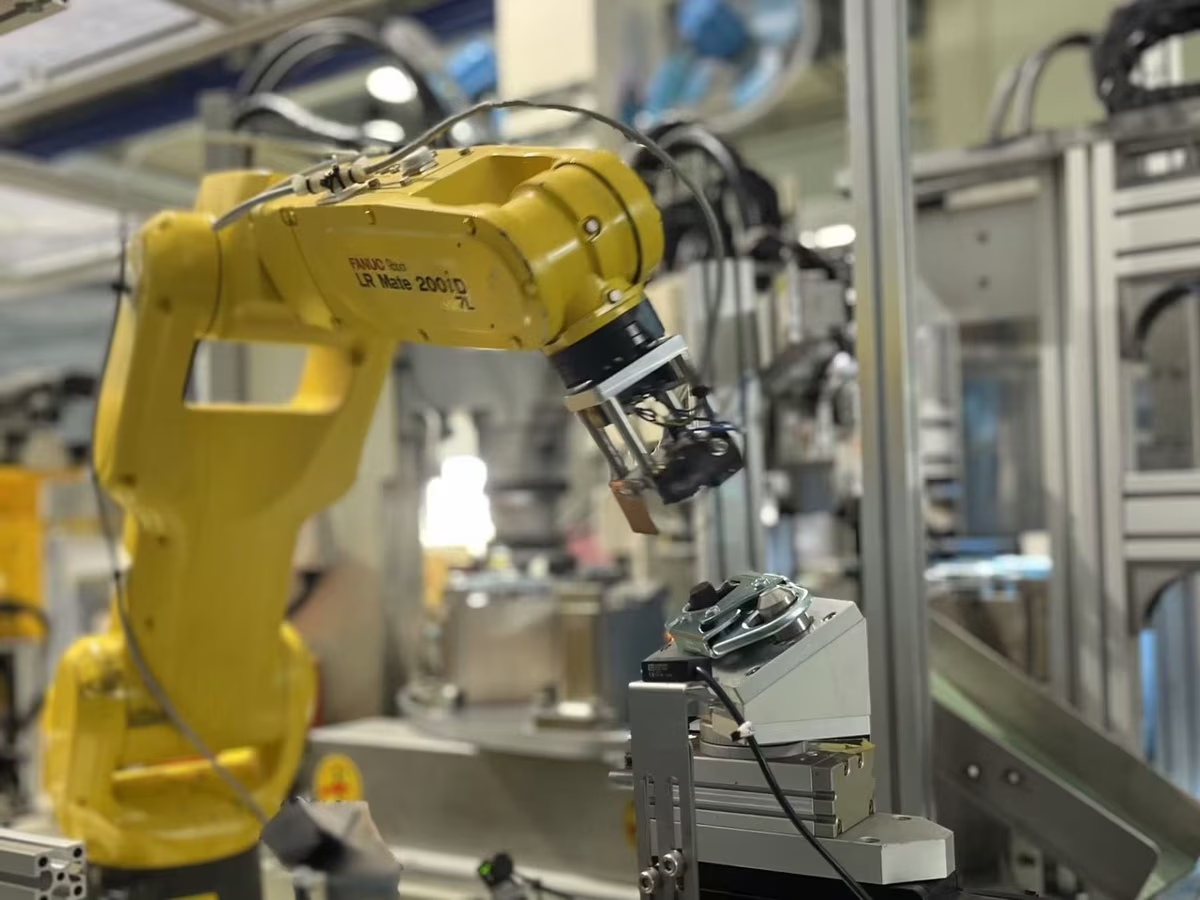
A bifocal modernisation strategy, implemented in 2011, is ongoing at YOKE Industrial Corp.’s pioneering industrial lifting equipment manufacturing facility.
Production at YOKE Industrial Corp. started in 1997.
A lot has changed since, as we’ll explore. What hasn’t, is that there are long-term career opportunities in an ever-evolving manufacturing environment.
YOKE’s approx. 56,000 square-metre facility produces a staggering 20 million pieces per year. The smart factory is built on 71 automation systems with 108 robotic arms; it is an automated fleet of state-of-the-art Fanuc equipment, that represents approx. US$30m worth of investment. In October 2024, for example, the total time of robotics operation topped 5,176 hours.
Importantly, the factory, located in Taiwan, also employs 500 employees, while human workforce numbers globally are on a steady upward trajectory. As Steven Hong, the company’s president, says, “We aim to achieve regional business services through the expansion of expatriate staff.”
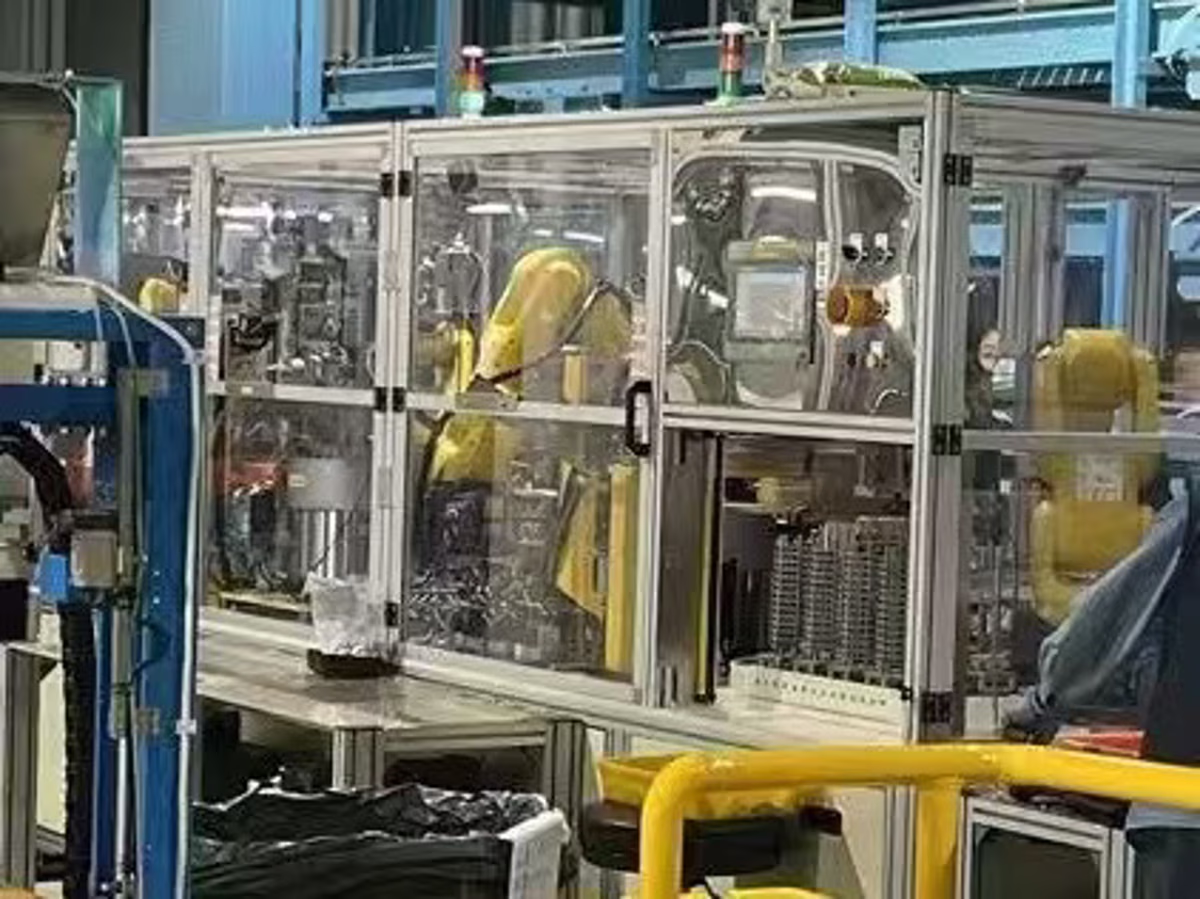
It’s been nearly 14 years since Hong took what was an unprecedented step at the time, into the world of robotics, with a two-tiered belief that still endures today:
- A fast in-and-out operational mindset.
- The companies that can solve handling and fast inventory management in the future will be the winners.
The first automated function was related to stacking finished products onto pallets — and it is still performing the same task today. With the benefits evident, automated storage and line-side storage systems were soon installed, and they were joined by unmanned automated guided vehicles (AGVs). Automated optical inspection (AOI) and automatic measurement systems were later installed for inspecting and measuring items during production processes. Automated systems for personnel assembly, and more loading / unloading technology were all added over the years that followed, principally to improve product quality and stabilise production quantity.
Even today, a dedicated department is constantly evaluating and designing future smart factory installations.
“The pace of automation implementation will never stop,” says Hong, “And many people are discussing the feasibility of introducing automation into various processes every day.”
Despite such a wholesale commitment to robotics and automation, YOKE staff numbers have not decreased.
“On the contrary,” says Hong. “Because of the expansion in production capacity, we have continued to add staff. However, the criteria for recruitment has changed, due to modifications in production and management models.”
The overall operation serves as proof that humans and robots are most efficient together. The automation systems introduced by YOKE are aimed at stabilising product quality, reducing reliance on personnel, and enhancing the value of employees. While production efficiency may not necessarily always improve, as robots are difficult to fully replace human hands, the benefits are clear:
- Stable quality
- Stable production volume
- Enhanced employee value
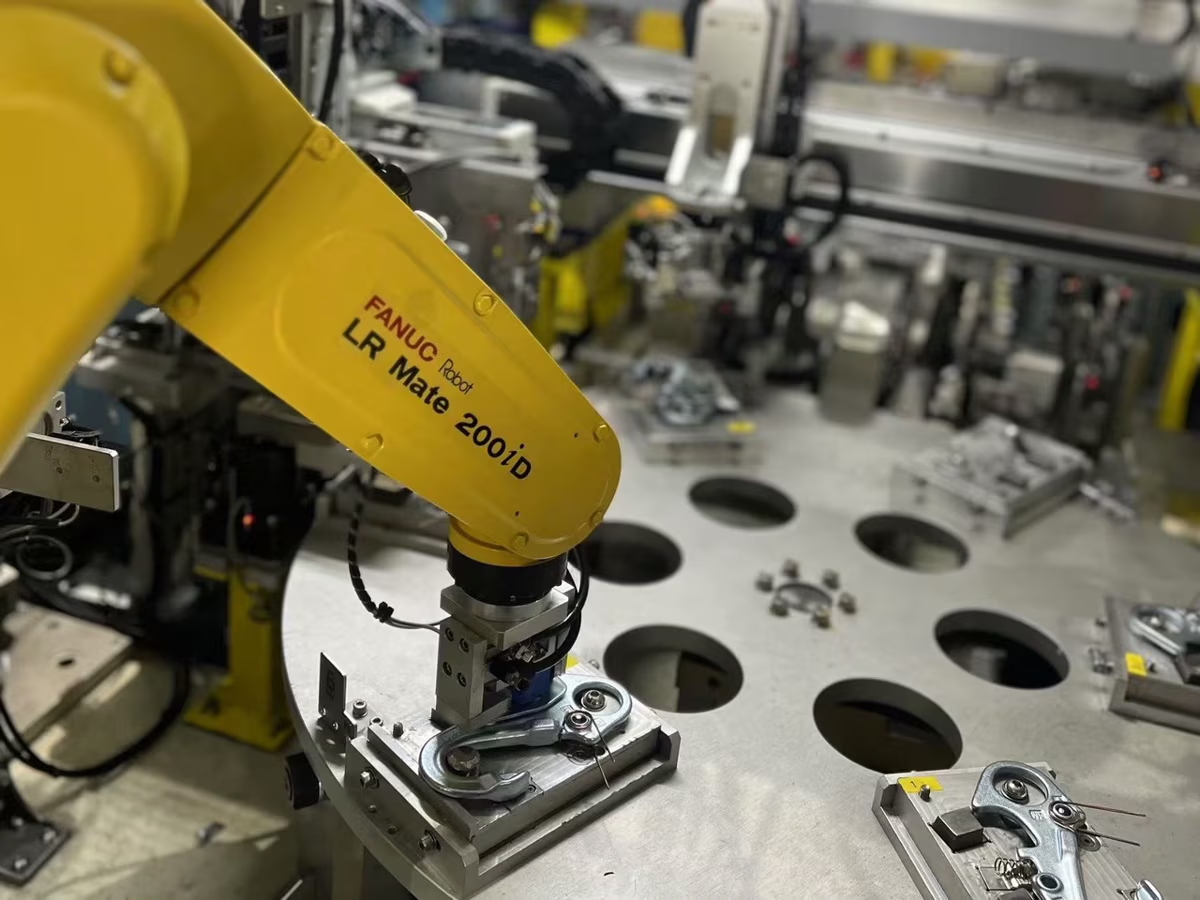
Exposure to new technological systems enables employees to operate complex equipment and manage multiple machines. This transition from monotonous tasks, such as loading and unloading, to operating machinery enhances the value of their work. Creating a dynamic, fast-paced, technology-driven environment, also engages a younger demographic of recruits. Many roles are directly related to automated processes; professionals are responsible for the design of moulds and fixtures, while personnel are involved in project evaluation for automation implementation.
“The smart factory environment does appeal to younger people,” says Hong. “The younger generation is more inclined to engage with new technologies and automation systems. This kind of working environment also offers opportunities for learning new skills and challenging themselves, which attracts more talent to join us.”
Any business looking to introduce automated systems must continue to value the human workforce. One of YOKE’s many strategies is a company-wide suggestion and improvement project, which has been in place since 2021. All employees, regardless of role or hierarchy, are invited to submit proposals each month on topics such as reducing production costs; improving quality; enhancing efficiency; process improvements; eliminating waste; enhancing workplace safety; energy-saving; etc.
Hong explained, “Department heads form a proposal review committee, and they select the top three proposals each month for rewards. Award-winning cases are announced to encourage all employees to follow suit. Everyone in YOKE can use this platform to raise any issues or suggestions related to production or environmental improvements.”
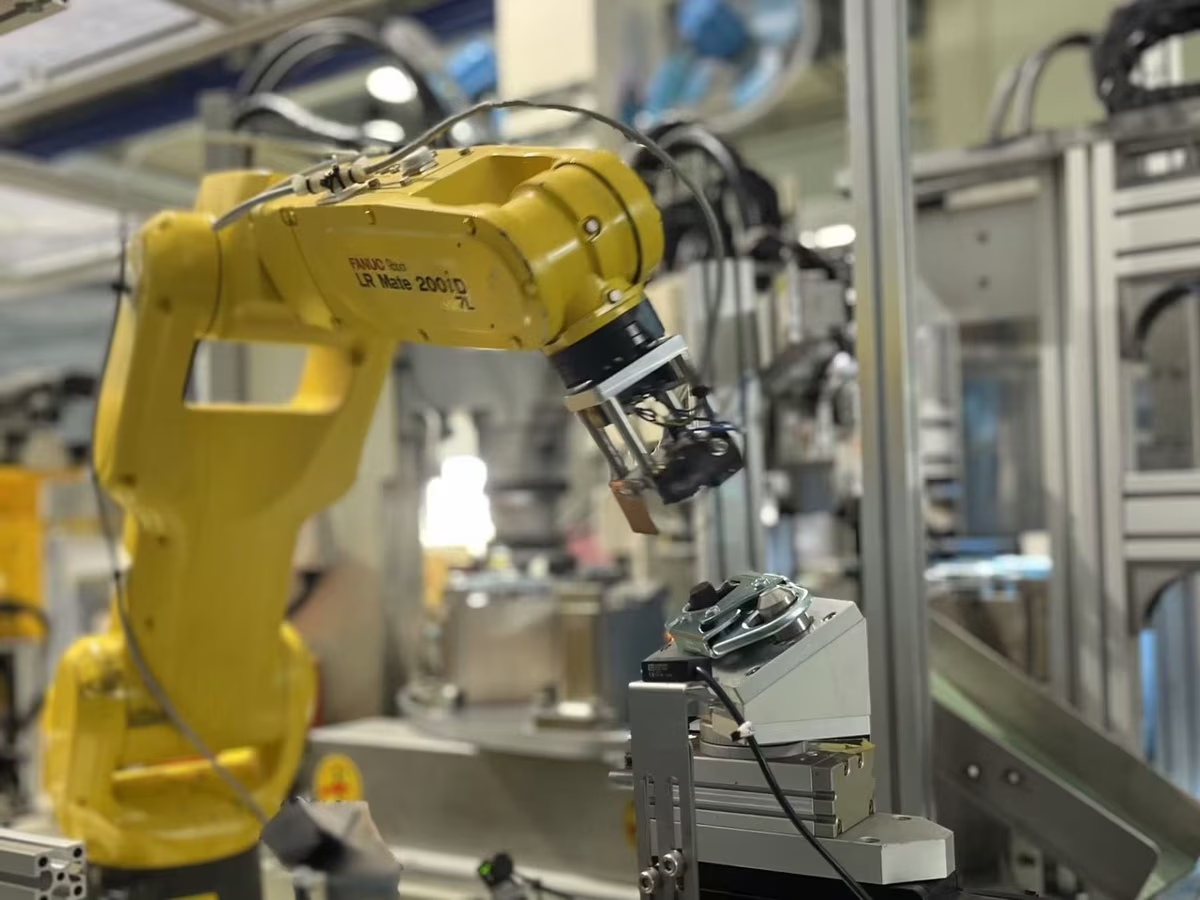
Climb to the summit
As YOKE’s fleet of robots has grown — from those stacking finished products onto pallets to AOI and everything in between — so too has the prevalence of the Fanuc logo, the iconic badge of the Japanese robotics company. Fanuc is one of the largest industrial robot manufacturers in the world, holding approximately 30% of the global market share. It is located at the foot of Mount Fuji in Japan, with over 5,000 robotic arms in use at its facility.
Hong says, “YOKE believes in the compounding effect of strong partnerships, and trusts that Fanuc can provide appropriate solutions for each manufacturing process as we implement automation. We are committed to advancing manufacturing by integrating both automation and digitalisation. We believe digitalisation is essential for improving efficiency, product quality, and staying competitive in the future. By implementing smart sensors, cloud-based platforms, and data analytics, we can optimise production processes and make data-driven decisions. While not claiming to be the sole leader, we strive to be at the forefront of this digital and automation transformation in the industry.”
YOKE’s growth, through robotics and ongoing personnel recruitment, is an example to follow for other manufacturing businesses, in lifting and other sectors.