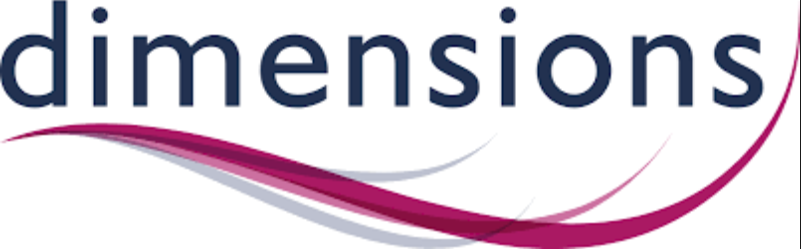
More businesses than ever before are having to introduce personal protective equipment (PPE) as part of a safeguarding focus of their operations. Earlier this year, the PPE Directive 89/686/EEC was replaced by the Regulation 2016/425 in a bid to improve health and safety at work.
As a result, professionals both in the UK and EU are having to revaluate their safeguarding procedures. Opposed to the former directive, the new regulation is a binding legislative act that must be applied in its entirety across the EU without requiring separate national legislation.
With technological advancements occurring throughout different industries, companies are adopting new innovations to better the productions — in terms of machinery and uniforms. Because of this, changes were required and expected to occur around PPE after it first came into action over two decades ago.
The PPE Directive which many businesses have grown to know previously focused on manufactures who placed items within the market. However, this new regulation that was put into action on 21st April 2018 will involve the entire supply chain. As a result, anyone who is part of the supply or distribution chain must abide by PPE and meet the standard requirements that have been set out — while also having an understanding that only products that meet the standards will be made available on the market.
The Standards That Must Be Followed:
- Making sure PPE complies with the essential health and safety requirements.
- Making sure technical documentation has be drawn up.
- When compliance has been demonstrated the EU declaration of conformity has been drawn up and a CE mark affixed.
- Retention of documents for ten years.
- Sample testing.
- Duty to take action in relation to non-conforming PPE.
- Labelling requirements.
- Providing instructions and cooperating with the national authority.
The transition period will end on the 21st April 2019 means that the previous Regulation will come into full force. However, any EC type-examination certificates and approvals issued under the Directive will remain valid until the 21st April 2023 unless they have an earlier expiry date.
PPE Categories
When taking a closer look at PPE, there are three categories which determine which workwear is needed.
Category I:
Simple design — this is where employees assess the protection they require for minimal risk jobs. For example, this could include the likes of garden gloves and ski goggles.
Category II:
Neither simple or complex — this is the middle ground for workwear that does not fit within Category I or Category III. For example, this could include wet suits!
Category III:
Complex design — this type of workwear has been designed to protect workers from dangerous tasks. For example, this could include harnesses and respiratory equipment.
PPE Compliance
Businesses may be compliant and supply their workers with the right workwear, but are employees wanting to wear it? Figures have suggested that 98% of employees have seen colleagues not wearing PPE when they were supposed to, with a further 30% saying this happens on a regular basis. Excuses varied as to why employees were not wearing the appropriate workwear with some suggesting that it looked unattractive, made them too hot, was a poor fit and was not very practical which should most definitely not be the case for such corporate workwear.
Did you know that 9% of all injuries are head injuries because 84% of such occurrences have not been wearing the proper headwear? Or that 50% of construction workers experience a serious injury during their career? If workers wore proper safety eyewear, injury could be reduced by up to 90%.
If safety gloves were worn for example, did you know that hand injuries could be reduced by 60%? 25% of employees are exposed to noise that are higher than the recommended level too, but such damage can be reduced 99% by wearing the right type of hearing protection.
Advice from business wear company Dimensions believe that it’s important for businesses to begin educating their staff on why this type of workwear is necessary for their safety. However, businesses must also take away from this article that workers feel uncomfortable in the PPE workwear that has been distributed to them – you must strike a balance between safety requirements and comfort to ensure that staff wear such equipment when needed.