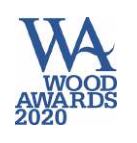
The winners of the annual Wood Awards have been announced. The judges have selected six structures and three products that represent the best of British architecture and product design in wood. Established in 1971, the Wood Awards is the UK’s premier competition for excellence in wood design. The competition is free to enter and aims to encourage and promote outstanding timber design, craftsmanship and installation.
The Wood Awards is one of the few design competitions to go ahead despite COVID-19. The independent panel of judges always visits all the shortlisted projects in person, making this a uniquely rigorous competition. This year, the usual judging process had to be adapted, but the competition persevered, and the judges still managed to see each project.
GOLD AWARD & PRIVATE WINNER
The judges chose The Rye Apartments as this year’s Gold Award and Private category winner. The Gold Award is given to the winner of winners. Judge Jim Greaves comments, “Tikari Works have taken a gamble and done
something very unusual and it’s paid off, the apartments are very popular.”
Location: London
Architect: Tikari Works
Structural engineer: Webb Yates
Wood supplier: Stora Enso
CLT subcontractor: Eurban
3-layer board: Binderholz
Species: Austrian spruce
©JackHobhouse
This development of ten sustainable apartments sits on a prominent corner site. A mix of one, two, and three-bedroom units are set in two blocks that respond independently to the changing scale across the site. The user’s quality of life is at the heart of the design. The project was driven by two key considerations; how to resist standardised or default positions within housing design, and how to minimise the materials, embodied carbon and cost. CLT was used for the superstructure and all the internal walls and staircases. The CLT is exposed throughout, creating large, light-filled spaces and a comforting atmosphere. These volumes are detailed with white-washed ash floors. Delicate spruce strips form dropped ceilings in the hallways and bathrooms. Kitchens cabinets are made from CNC grooved three-layer spruce ply boards and the worktops are made from recycled paper. The limited palette of natural materials helps to minimise visual clutter.
COMMERCIAL & LEISURE
The Commercial & Leisure winner is Frindsbury Manor Barn. The judges admired the attention to detail and scale of the conservation project.
Location: Rochester
Architect & client: The Heritage Design & Development Team Ltd
Structural engineer: The Morton Partnership
Main contractor, joinery & wood supplier: Dolmen Conservation Ltd
Species: British oak
This Grade 1 listed medieval barn, originally built in 1403, was damaged by fire in 2003. At 210 feet long it is the longest barn in the UK. A third of the barn was re-built in locally sourced green oak. Large quantities of curved timber were selected for braces and tie beams. In total, 1400 f3 of oak was used. Extensive stone repairs were also needed. 95,000 Kent peg tiles were used to re-tile the old and new sections of the barn. The project was based on the fundamental principles of conservation: ‘maintain as much of the historic fabric as possible whist ensuring the building has a viable future use’. The barn and its surrounding areas are steeped in history and it remains fundamental to the local community.
EDUCATION & PUBLIC SECTOR
Swimming Pool Hall at King’s College School, Wimbledon was selected as the Education & Public Sector winner. Judge Kirsten Haggart says, “The different timber elements all have the same white-washed tone and coordinate
perfectly with the reinforced concrete columns, creating a beautiful place which has an intimacy that most pools lack.”
Location: Wimbledon
Architect: David Morley Architects
Client: King’s College Wimbledon
Structural engineer: Price & Myers
Main contractor: Knight Harwood
Timber contractor: B&K Structures
Joinery: Suffolk and Essex Joinery Ltd
Wood supplier: Metsa Group Ltd
Species: spruce, pine, fir, larch (European)
The Swimming Pool Hall is one of three linked pavilions comprising a new sports centre for the school. The building’s design has strong visual connections between indoors and outdoors to encourage physical activity among students whilst seamlessly connecting the old facilities. The form of the roof evokes a dynamic sense of movement in water. From outside, it sweeps down to respect the boundary with a Grade 2* listed building. Internally, it sweeps up to accommodate a viewing gallery. Curved glulam beams support CLT roof panels with integral timber acoustic linings. The roof’s geometry and pale stained finish reflect natural top-light and artificial uplighters, eliminating the need for any light fittings above the pool. The flush pool edge and glazing on three sides allow views to the outside.
INTERIORS
The Interiors winner is Brockeridge Stair. Judge Ruth Slavid comments, “This is a very beautiful and impressive stair. In addition, there is a great story in that it was used to pioneer an approach to the use of BIM in joinery manufacture that is the recipient of ongoing government grants.”
Location: Bristol
Staircase & joinery design: Future Joinery Systems Ltd
Architect: CaSA Architects
Structural engineer: Mann Williams
Digital fabrication: FabLab Cardiff, Cardiff Metropolitan University’s School of Art & Design
Joinery: Silverthorne Joinery & Carpentry
Wood supplier: Hanson Plywood Limited
Species: ash, birch
This prototype staircase is part of a UK government funded R&D project to enable digital fabrication directly from BIM modelling environments. The stair rises three floors and is cantilevered from flush mounted stringers. The parts were CNC machined and assembled onsite using standard tools. The new platform developed during research allows designs to be defined parametrically, enabling the user to configure bespoke objects to specific requirements. Parameters such as height, width, depth and material thickness can be user controlled. Digital manufacturing is enabled directly from CAD or BIM software via the platform which enables faster fabrication, better pricing information and reduces errors and waste. Items can be locally fabricated through a distributed manufacturing network model open to any CNC enabled workshop. The process greatly improves construction efficiency, supports COVID-19 social distancing restrictions, increases the type and complexity of work undertaken by smaller site-based joiners, and keeps the labour pool local.
SMALL PROJECT
This year’s Small Project winner is Wooden Roof. The judges were impressed by the light and airy garden room and were particularly interested in the process of design through to construction.
Location: London
Architect: Tsuruta Architects
Structural engineer: Webb Yates
Main contractor: JK London Construction
Joinery: Pracownia Wystroju Wnetrz Art Deco -R
Wood supplier: Arnold Laver
Species: Accoya (New Zealand), ash (Canada)
This conservatory, built for an existing Grade 2 listed house, sits in a north-facing garden. The roof profile had to be pitched shallow to ensure that it sits below the existing adjacent boundary wall shared with the neighbour. The roof also needed to be well- drained. One solid piece of wood, enclosed by four seasons glazing units, forms the entire structure and acts the building’s envelope, structure, insulation and cladding. The diagrid frame is a combination of falls that are either short and steep or long and shallow. The pieces were all CNC fabricated and were light enough to be assembled manually onsite. The beam cross junctions were fixed without any glue or mechanical fixings. Each wood section is wide and deep which helps to emphasise natural light and cast shadows throughout the space.
STRUCTURAL AWARD
This year’s Structural Award winner is the National Automotive Innovation Centre, chosen from all the shortlisted buildings. Structural judge Nathan Wheatley comments, “We are looking for a scheme that has challenged the engineer, where the concept has been delivered in spite of that challenge and where the resultant structure is in some way integral to the success (and architecture) of the building.”
Location: Coventry
Architect: Cullinan Studio
Client: University of Warwick
Structural engineer: ARUP
Main contractor: Balfour Beatty
Joinery: B&K Structures
Quantity surveyor, cost consultant & project manager: Rider Levitt Bucknall
Timber engineer: engenuiti
Wood supplier: Rubner Holzbau Gmbh, Ober-Grafendorf, Binderholz
GmbH
Species: CLT, spruce glulam (European)
©HuftonCrow
The National Automotive Innovation Centre is the largest research and development centre of its kind in Europe. It can hold 1,000 staff and students working across design, engineering and research. Timber was chosen for its warm, natural feel within the industrial setting and its wellness and low carbon properties. The walls were assembled using a pioneering system of prefabricated, self-spanning timber and CLT mega-panels that could be erected quickly. As one of the largest timber roofs in the world, the glulam CLT lattice structure unifies the many activities housed beneath a single umbrella. Primary and secondary joists are arranged on a diagrid, spanning onto supporting beams on a 15m grid. Each bay is slightly pitched above to create a nominal fall for the roof, tapered internally within each bay. The undulating soffit profile draws users through the space.
BESPOKE FURNITURE
The Furniture & Product judges selected two winners within the Bespoke category.
Duo by Studio Woodgate were awarded for their elegance, simplicity and exemplary craftsmanship.
Designer: Studio Woodgate
Maker: Benchmark Furniture
Client: Royal Opera House as part of ‘Legacy’ for LDF 2019
Project facilitator: AHEC
Wood supplier: Morgan Timber
Species: American red oak
©PetrKrejci
Duo is a pair of deceptively delicate sofas designed for Alex Beard CBE, Chief Executive of The Royal Opera House. When first tasked with project, Woodgate started by observing the space at the Royal Opera House. He noticed that the existing sofas were the same height as the chairs in the room. A lower sofa would create a different dynamic to the room. Conscious not to make the sofas too comfortable, the approach was to create something more comfortable than a bench but not as soft as a sofa. The light rectangular arms have a curved chamfer detail with cleverly hidden metal rods to ensure the sofa is robust. A subtle 2 millimetre radius runs around the edge of the wood throughout the piece. The two end frames for the arms were made up from solid timber and shaped on a 5-axis CNC machine. The seat and back are made from a solid timber frame and sit on a nook cut into the end frames secured by a metal dowel. The seats are upholstered in tan leather.
The Beehave by Marlene Huissoud was recognised for its unusuality and the attention to detail that went into the making of it. The judges also praised that it is a fully functioning behive and not just a sculptural piece.
Designer: Studio Marlene Huissoud
Maker: Benchmark Furniture
Client: Science Museum London as part of ‘Legacy’ for LDF 2019
Wood supplier: Morgan Timber
Species: American red oak
Sir Ian Blatchford commissioned Marlène Huissoud to create a beehive to feature in a new permanent gallery at the Science Museum focused on the future of agriculture. Whilst doing research, Ian came across a study focused on the habits of bees and the reason behind their decline in population. Marlène’s artistic outlook is rooted in the natural world. She also the daughter of a beekeeper. Rather than a traditional, house-like beehive, Marlène created something more organic. The log-like hive is a refuge for wild bees rather than place to make honey. The piece was hand carved and the red oak was then blackened using a scorching technique. It took 100 hours to add the tactile engraving details to the surface using a pyrograph. It was then covered with propolis, a dark resinous material produced by bees, to seal the gaps. This protects the timber and the bees from disease and also attracts bees with its scent.
PRODUCTION FURNITURE
Tenon Table is the Production winner. The judges admired the design and were particularly impressed by how well balanced the tables are.
Designer: Daniel Schofield
Manufacturer: L.Ercolani
Wood species: ash, oak (Italy)
Designer Daniel Schofield has taken a pragmatic approach to the design of the Tenon Table. Material has been removed where it is not needed, leaving the base weighted and stable which naturally creates the joint for the top. The oversized wedged tenon has become a focal point which highlights the construction of the piece and the quality of craftsmanship. A combination of wood turning, CNC machinery and hand jointing have been used to create each piece. The table is available in two sizes.
JUDGES
The buildings judging panel is led by three-time Gold Award winner Stephen Corbett of Green Oak Carpentry. The panel includes Andrew Lawrence, Arup; Kirsten Haggart, Waugh Thistleton Architects; Nathan Wheatley, engenuiti; David Morley, David Morley Architects; Jim Greaves, Hopkins; and architectural journalist Ruth Slavid. The furniture and product panel is led by design critic, curator and journalist Corinne Julius. The panel includes Oliver Stratford, editor of Disegno magazine; Rod Wales of Wales & Wales; and previous winners Yael Mer of Raw-Edges, Eleanor Lakelin and Sebastian Cox.
SPONSORS
As a not-for-profit competition, the Wood Awards can only happen with collaborative industry sponsorship. Major Sponsors are American Hardwood Export Council and Carpenters’ Company. Other Sponsors include American Softwoods, Timber Trade Federation and TRADA.