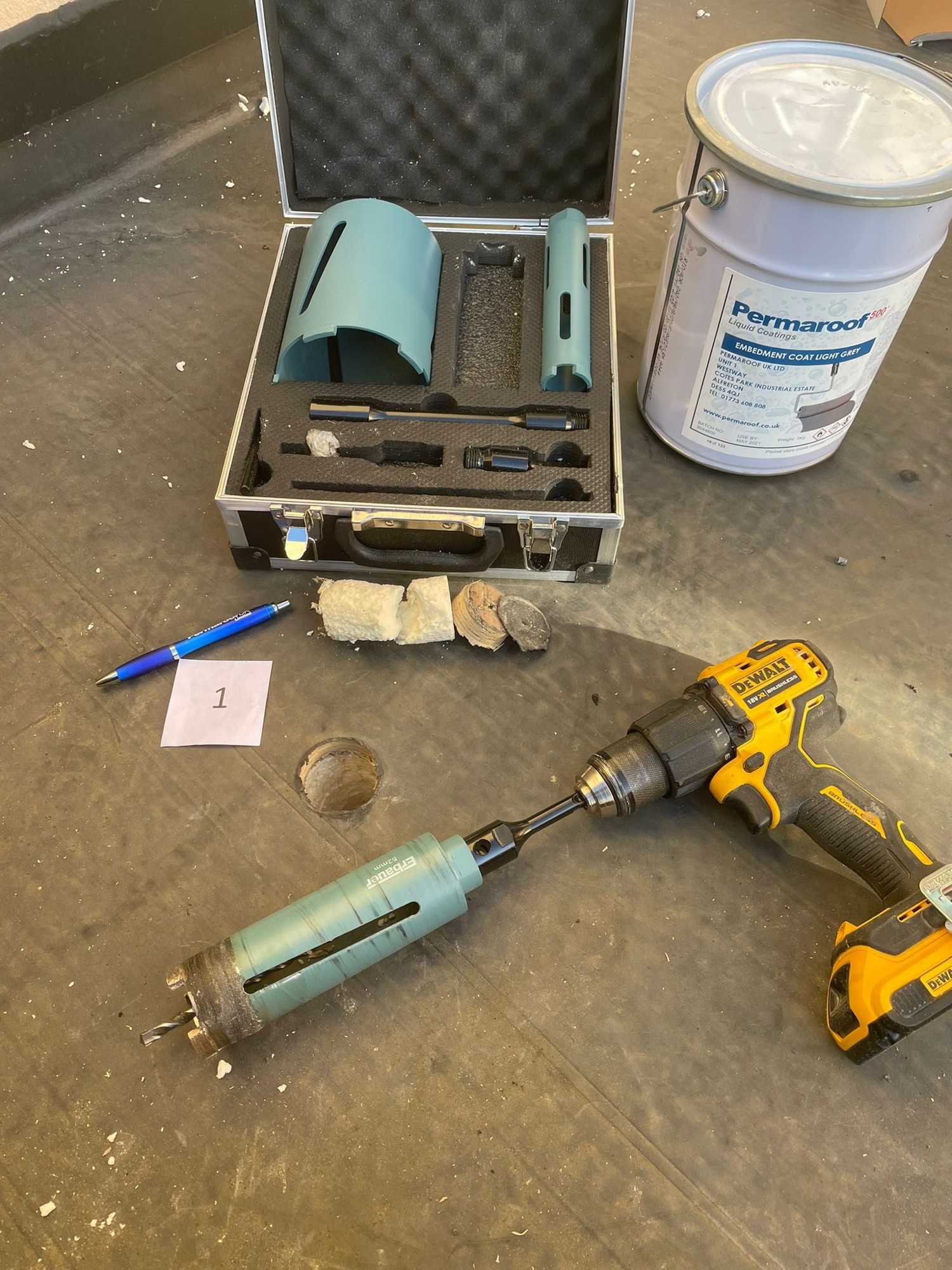
Replacing a roof can be a costly and time-consuming job, but one that cannot be avoided or overlooked if it has reached a state of disrepair. Something that can often be overlooked, however, is a flat roof survey. Due to the simple fact that people tend to wait for problems to arise before addressing them.
But a survey can often mean the difference between extending a roof’s lifespan, removing the need for a replacement, and its failure. Sunny Lotay, national commercial manager at PermaRoof UK, gives an overview of the processes involved with and the benefits of incorporating this service into a flat roof’s life cycle.
Flat roof surveys are undertaken to determine what the condition of an existing roof is and to pinpoint any problems or areas of concern such as waterproofing and structural issues, flashing problems, ponding water and much more. If left unidentified, or not resolved quickly and efficiently, these issues can have a long-term impact on the lifespan and structural integrity of the roof, leading to costly repairs or even premature failure.
While these surveys are generally performed visually, there may be certain cases that require some intrusion – such as core sampling – into the existing structure to help identify issues lying beneath the surface.
This assessment then informs and determines the correct flat roof system proposal to put forward. These could include a number of measures or fixes, such as thermal upgrade options, structural and drainage improvements, maintenance access walkways or fall arrest systems – to name just a few.
Preparation is key
While people tend to wait until a problem occurs or, in some cases, just before a major project is about to start to have a flat roof survey undertaken – it’s best to opt for a more proactive and consistent approach.
A general annual check can help to minimise the possibility of issues developing and identify the areas that may only require some quick repairs or maintenance. As a rule of thumb, flat roofs should have a twice-yearly check to clear any debris or outlet blockages, ensuring the longevity of the roof and that it remains watertight for years to come.
In addition, as roofs age and issues start to occur, it is generally imperative that a roof survey is conducted as quickly as possible to determine when a replacement will need to be made and to afford enough time to identify the correct system build and compliance is met.
While there’s not technically a ‘best’ time of year to have a roof survey done as it generally depends on a variety of factors, not least the condition of the roof, I would often recommend precautionary surveys be taken in the time leading up to late spring or summer. This allows time for any potential repairs to be made before the wet winter months take hold.
The process
Surveys can include a number of elements, from checking thermal regulation and fall of water discharge to structural soundness and whether there are enough outlets. Depending on the results of the survey, there might not be any action required. Therefore, when finding a specification manager to carry out the survey, it’s important that you opt for someone who is able to offer a no obligation, completely free of charge survey, core test and condition report, like PermaRoof.
There are a number of factors that need to be considered when preparing to conduct a roof survey, from checking the weather and ensuring all of the correct equipment is to hand through to what health and safety measures need putting in place and following during the time on site.
Depending on the roof size and complexity, a flat roof survey can take anywhere from a morning to, in some cases, a couple of days. Once the survey itself is complete, its time to compile the roof report and make the recommendations required. We strive to submit this within a week of completing the survey, in which we offer our proposal for the correct system and nominate three PermaRoof registered installers to quote for the project.
In practice
At a recent survey, a core test was undertaken at a residential block of flats in south London to ascertain the build-up of the existing roof. This test determined that it was a cold roof, with timber substrate and asphalt on top as the waterproofing element.
Through this report a recommendation was made to upgrade from a cold roof to a warm roof, using the existing asphalt roof as a vapour control layer, was specified. Consisting of a brand-new 120mm insulation layer, along with an 18mm OSB board and topped by the Firestone Rubbergard EPDM system, a watertight roof with a 20-year warranty was delivered – providing peace of mind for years to come, which would not have been the case without the survey being undertaken.
For more information on PermaRoof Commercial, please visit permaroofcommercial.co.uk, call 01773 608839 or email flatroofing@permaroof.co.uk.