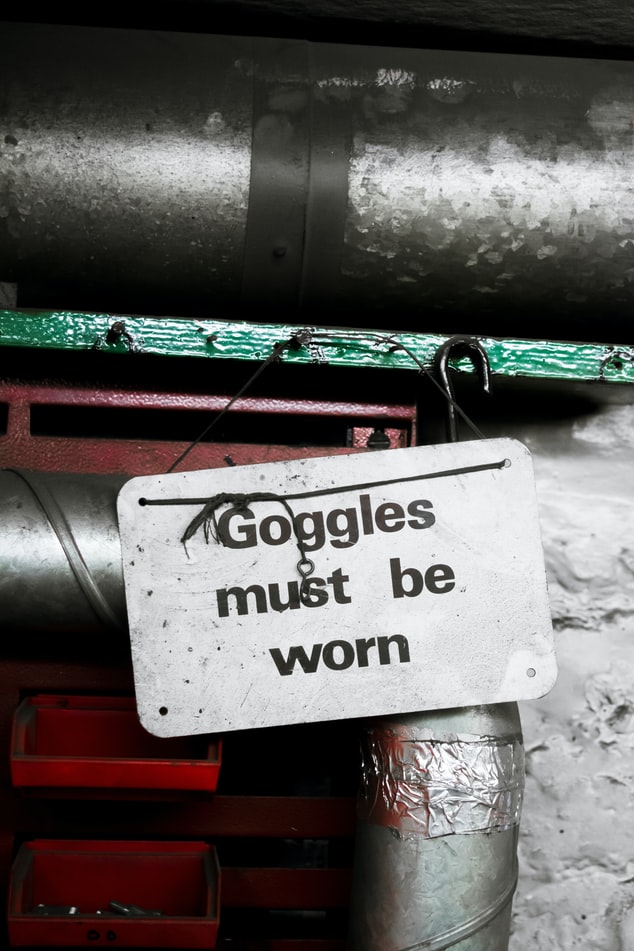
In workplaces throughout many different industries, there has long been a myth that productivity must be sacrificed for the sake of health and safety. The idea that health and safety is something that gets in the way of swift operational management is dangerous and, in reality, unfounded. In fact, high levels of health and safety are vital to operational efficiency, whatever sector you work in.
Read on as we get take this myth apart piece by piece and delve into the reasons why health and safety is absolutely necessary for operational efficiency.
A global perspective
If there’s one clear way to see the link between health and safety and operational efficiency, it’s by comparing different countries’ attitudes towards these factors.
The world’s most productive countries according to the Expert Market, including Luxembourg, Norway, and Switzerland, all have aspirational levels of health and safety. Studies have also shown a correlation between workplace health and safety standards and a country’s competitiveness within the global economy. Countries including Finland, the United States and Denmark all come out on top in both areas, with countries including Indonesia and Brazil on the other end of the scale.
The cost of accidents
It goes without saying that as well as endangering workers, accidents cost money. When accidents occur, employers have to account for multiple costs, such as:
- Workers’ compensation payments
- Medical expenses
- Noncompliance fines
- Litigation expenses
- Property losses
Not only do these things cost money – which is sure to have a direct impact on productivity as costs will have to be cut in other areas of the business – but accidents in the workplace due to poor health and safety will cost your business time.
According to Health and Safety England, 38.8 million working days were lost over 2019/20 due to work-related illness and workplace injury. Improved health and safety measures in your organisation will help to prevent these injuries. In doing so, you will save days upon days of efficient operational time.
Operational downtime
Machine downtime is another factor to consider. Poor health and safety measures could include poorly-maintained machinery or people who are not feeling fit to operate heavy equipment. As well as this, the indirect costs of substandard health and safety include project delays, abrupt losses of skilled workers, and losing out on business deals.
If your company relies on heavy machinery, it should all be checked regularly as part of your health and safety review. Factors such as poor joint integrity, misaligned tighteners, worn parts and poor electrical connections can all create a safety risk which could be dangerous for your employees and cause serious setbacks in your processes.
Worker morale
High levels of health and safety are known to boost worker morale. After all, when an employee feels comfortable and safe in their workplace, and they trust their employers to consider their needs, they are likely to work harder and be much happier in their jobs.
It has been found that happy employees are 12 per cent more productive, and unhappy employees are ten per cent less productive – so it’s always worth considering your employees’ happiness, both for the sake of both overall worker morale, and greater productivity.
You must always keep in mind that safety and morale should be your priorities. Productivity should follow as a natural result. Studies have found that one in three workers believe that their employer values productivity more than safety, and if you think this might be the belief in your workplace, you need to work hard to remedy it. To ensure that your employees feel both safe and valued, you should update your health and safety procedures regularly, ask for regular feedback from your employees and listen to their views and opinions. You should also communicate clearly any regulations you have put in place to make the workplace safer.
Efficiency, productivity, health and safety, and worker morale should all form the backbone of your business. Any business owner who plans to skip ahead to the efficiency stage, allowing health and safety to fall by the wayside, is destined to fail. Put your workers’ needs first and watch how your business becomes more efficient than ever – happy workers are productive workers after all.
Sources
https://www.fastcompany.com/3048751/happy-employees-are-12-more-productive-at-work
https://www.hse.gov.uk/statistics/
https://www.expertmarket.co.uk/crm-systems/the-ultimate-guide-to-work-place-productivity