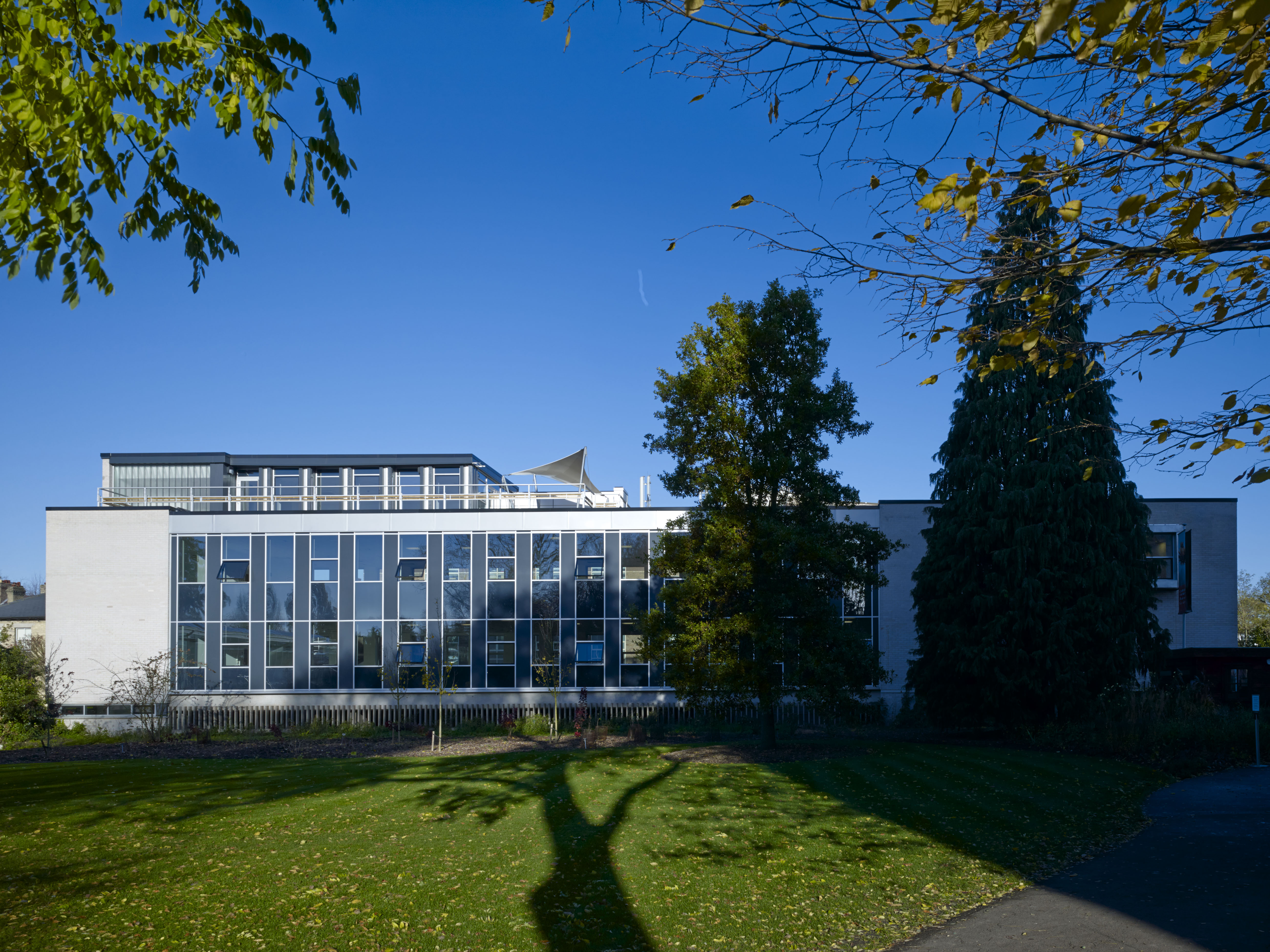
Curtain walling, windows and doors from Kawneer feature on a major office refurbishment.
Elements from the complete portfolio of glazing systems from leading architectural aluminium supplier Kawneer were specified for the major refurbishment of a derelict office building for their “good cost to performance balance”.
Kawneer’s curtain walling, windows, doors and framing systems were selected by Barber Casanovas Ruffles chartered architects for 90 Hills Road, Cambridge, which had been derelict for seven years.
The manufacturer’s AA®100 zone-drained curtain walling with narrower 50mm sightlines was used for screen and window replacement with AA®100 concealed window vents.
The £1.7million refurbishment for Freshwater Property Management also featured Kawneer’s 451PT framing system with series 190 heavy-duty commercial entrance and low/medium-duty swing doors.
They were installed on the three storeys of the 1960s building over four months by Kawneer-approved specialist sub-contractor Elliston Steady & Hawes (Aluminium) for main contractor Morgan Sindall.
The brief to Barber Casanovas Ruffles was to retain the quality architectural aspects of the building and work with the existing structure to bring it up to current office standards, considering its existing design, materials, fenestration, structure and urban context.
The external walls, floors and roof were upgraded, including creating a roof terrace on the second floor, to provide better thermal performance, while subtle modifications and additions to the fenestration improve daylight levels and energy efficiency.
The existing windows were completely replaced with Kawneer’s curtain walling inclusive of the opening windows which allow the building to be naturally ventilated by a mixed-mode strategy.
A spokesman for Barber Casanovas Ruffles, who have specified Kawneer for 27 years, said: “The product has a good cost to performance balance. With our design it improved the visual appearance of the building as the main facades are predominately curtain walling.”
The year-long build involved exposing the existing fabric back to the main structure (of in-situ concrete ground-floor slab with load-bearing masonry and a top floor of steel column and lattice space frame) where possible.
Removing the entire envelope and its reinstatement with modern and performance-related materials involved some technically challenging design detailing. The original façade had to be dismantled beneath a temporary full-building cover to ensure the internal surfaces remained dry during the envelope reconstruction.